Services
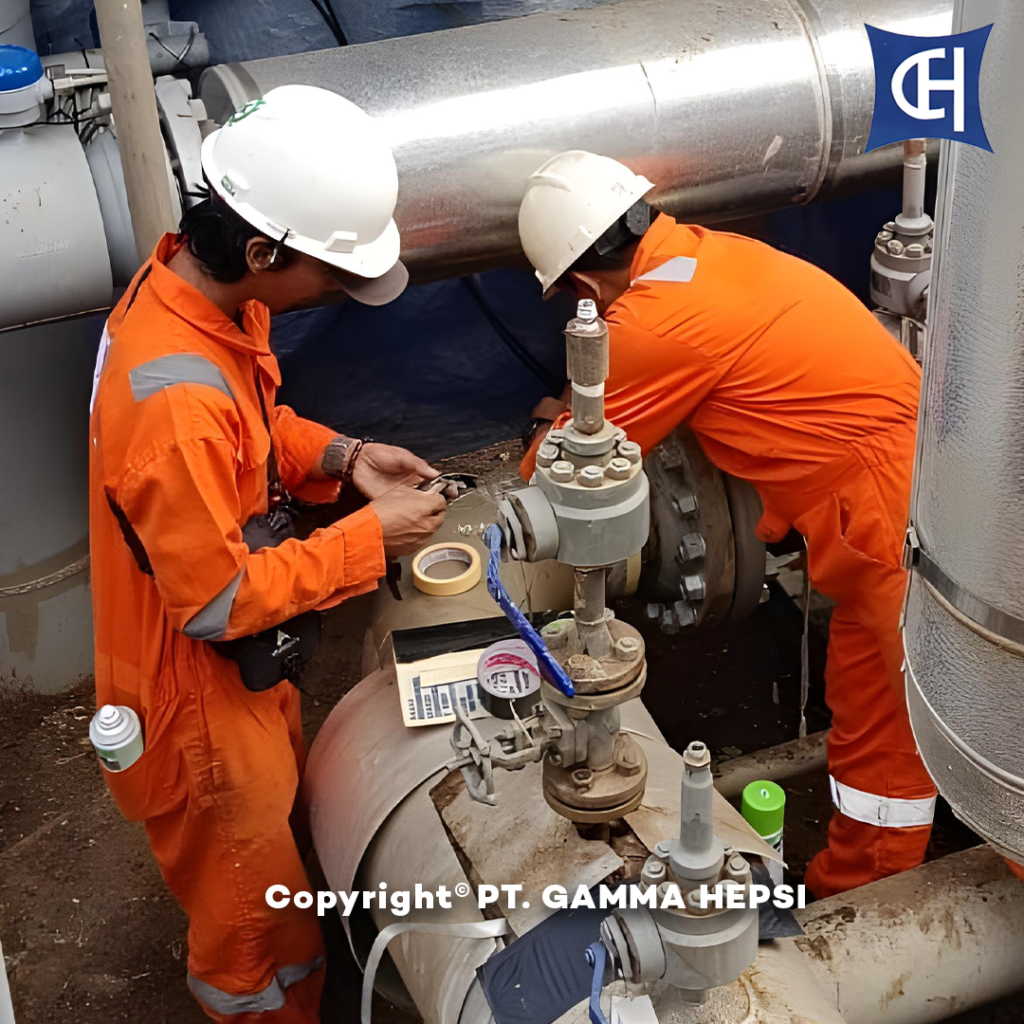
Radiography (Gamma Ray)
Click for detail
Radiographic inspection of pipes, which involves the use of Gamma Rays or X-rays, is a nondestructive testing (NDT) method employed to assess the integrity of pipes, identify defects, and ensure the structural reliability of the system. This method utilizes high-energy radiation to penetrate the material and capture images on a photographic film or digital detector. These images reveal internal flaws, such as cracks, corrosion, weld defects, or other discontinuities that could compromise the pipe’s functionality and safety
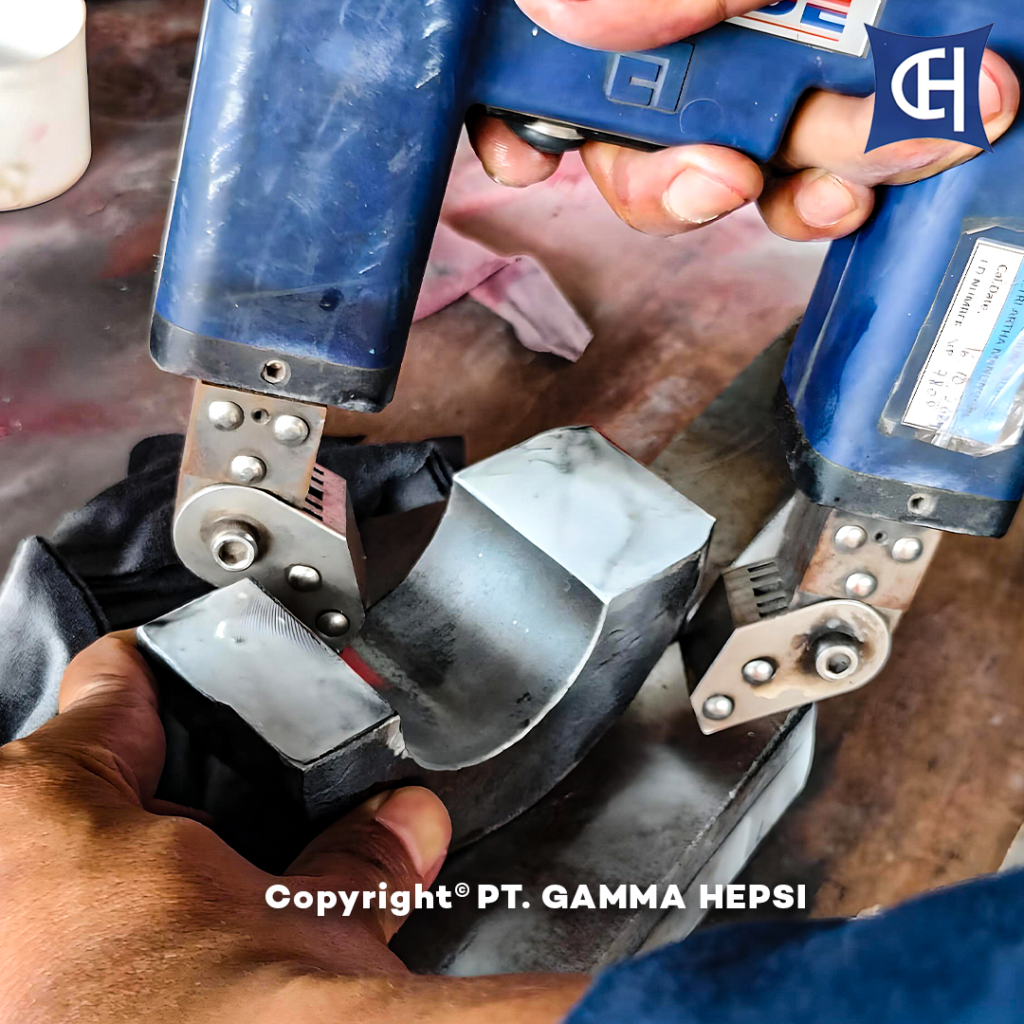
Magnetic Particle Inspection
Click for detail
Magnetic Particle Inspection (MPI) is a nondestructive testing (NDT) method used to detect surface and near-surface discontinuities in ferromagnetic materials, such as steel and iron, commonly used in pipelines. MPI is highly effective for identifying cracks, laps, seams, and other defects that can compromise the structural integrity of a pipe.
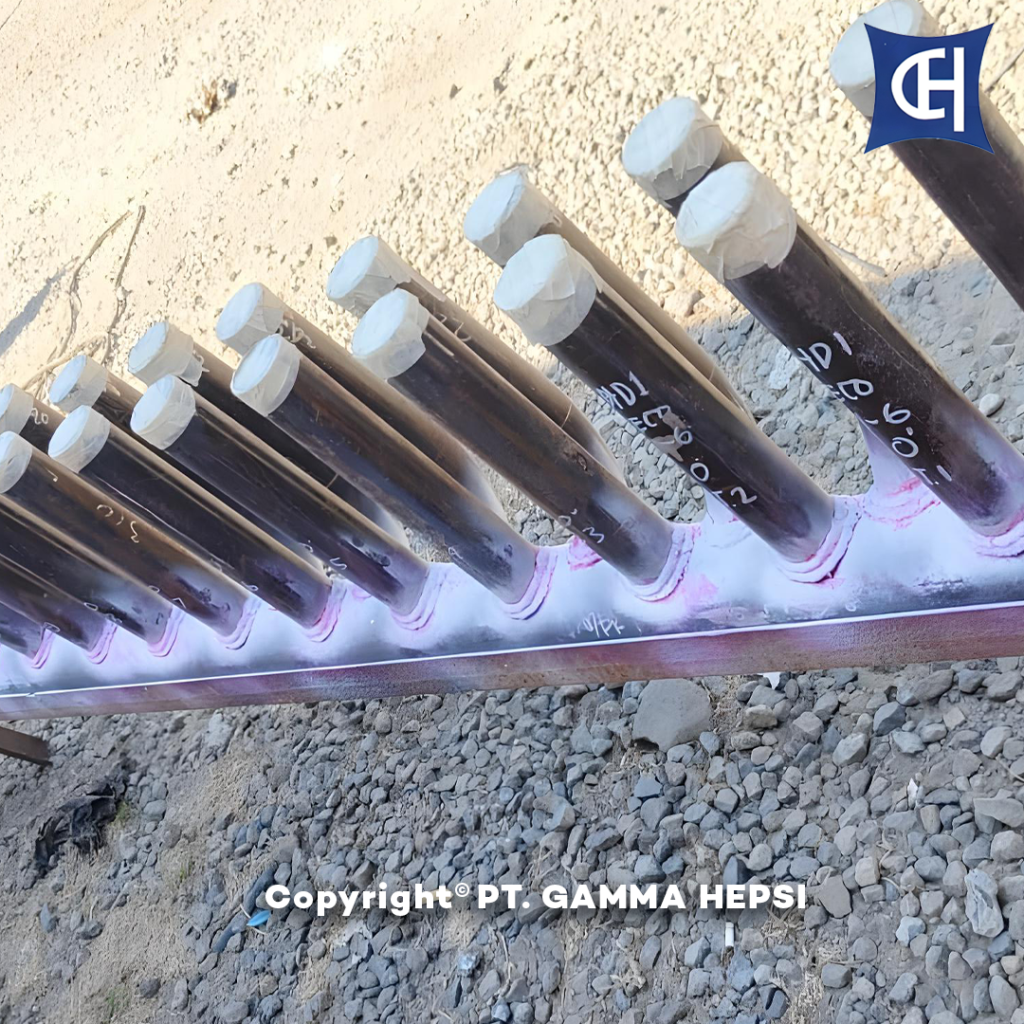
Liquid Penetrant Inspection
Click for detail
Liquid Penetrant Inspection (LPI), also known as Dye Penetrant Testing (DPT), is a widely used nondestructive testing (NDT) method to detect surface-breaking defects in materials, particularly in pipes and pipe welds. This method relies on the capillary action of a liquid penetrant to highlight flaws on the surface of a pipe, such as cracks, porosity, and other discontinuities.
LPI is highly effective for inspecting non-porous materials (typically metals and non-ferrous alloys) and is ideal for detecting surface defects like small cracks, leaks, or corrosion, which can be otherwise hard to identify using other inspection methods.
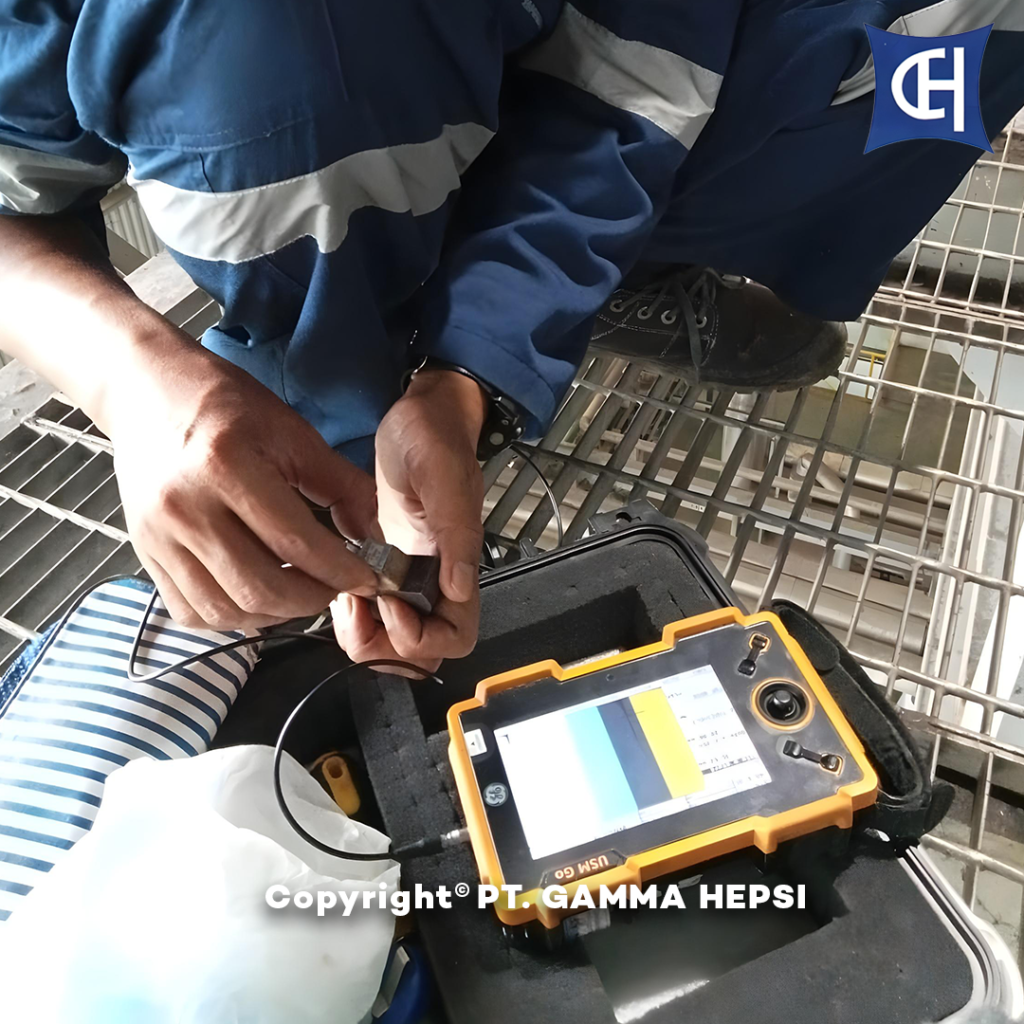
Ultrasonic Test
Click for detail
Ultrasonic Testing (UT) is a powerful and widely used Nondestructive Testing (NDT) method for inspecting the internal and external integrity of pipes and pipeline systems. UT utilizes high-frequency sound waves (ultrasonics) to detect internal flaws, measure material thickness, assess corrosion, and evaluate weld quality. It is effective for both thick-walled and thin-walled pipes and is commonly applied in industries such as oil and gas, nuclear, chemical, and petrochemical.
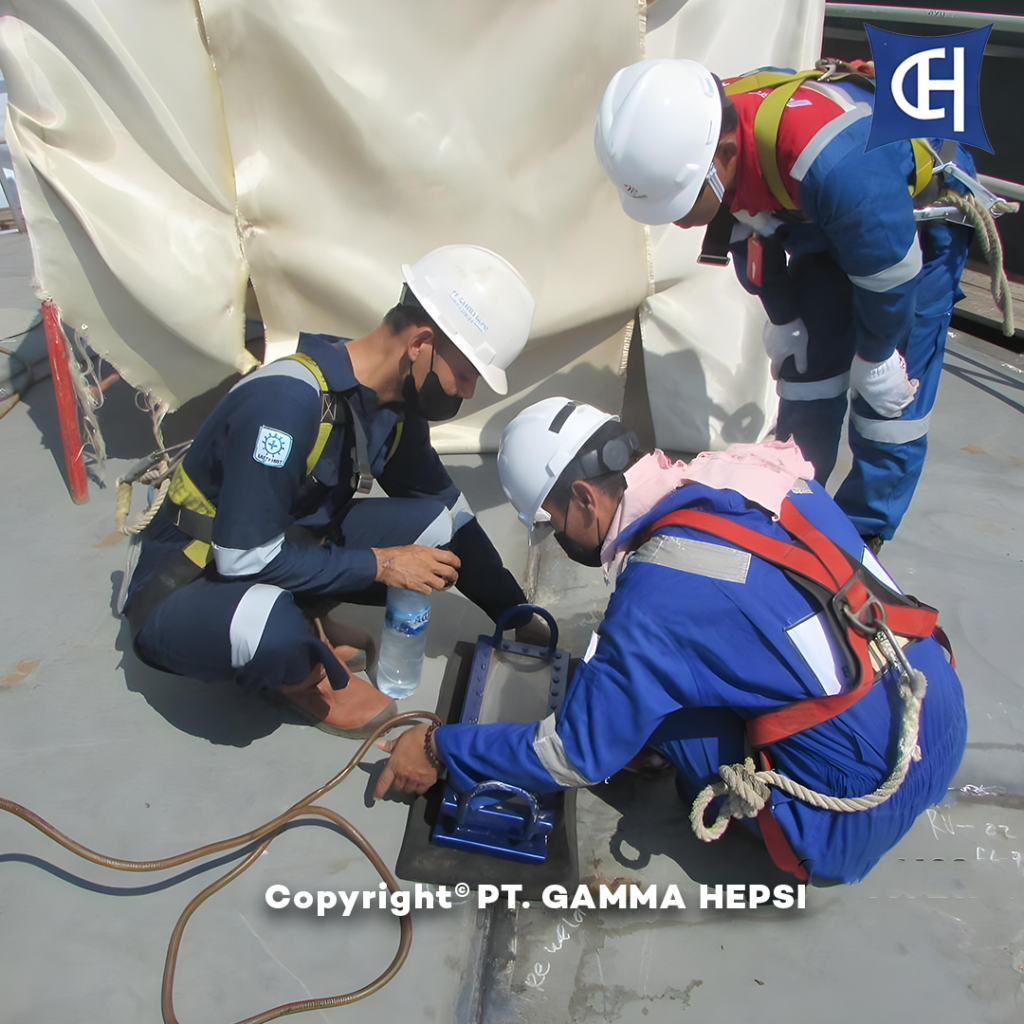
Vacuum Test
Click for detail
Vacuum Testing is a type of nondestructive testing (NDT) method used primarily to detect leaks or to verify the integrity of pipes, pipe joints, and welded areas. It involves applying a vacuum to the internal or external surface of the pipe or component and monitoring for any loss of pressure or leakage, which indicates the presence of defects.
Vacuum testing is commonly used in industries such as oil and gas, chemical processing, water utilities, and construction for both pre-service and in-service inspections of piping systems. It is especially valuable in systems where leakage can have serious consequences or when it is difficult to detect leaks using visual inspection alone.
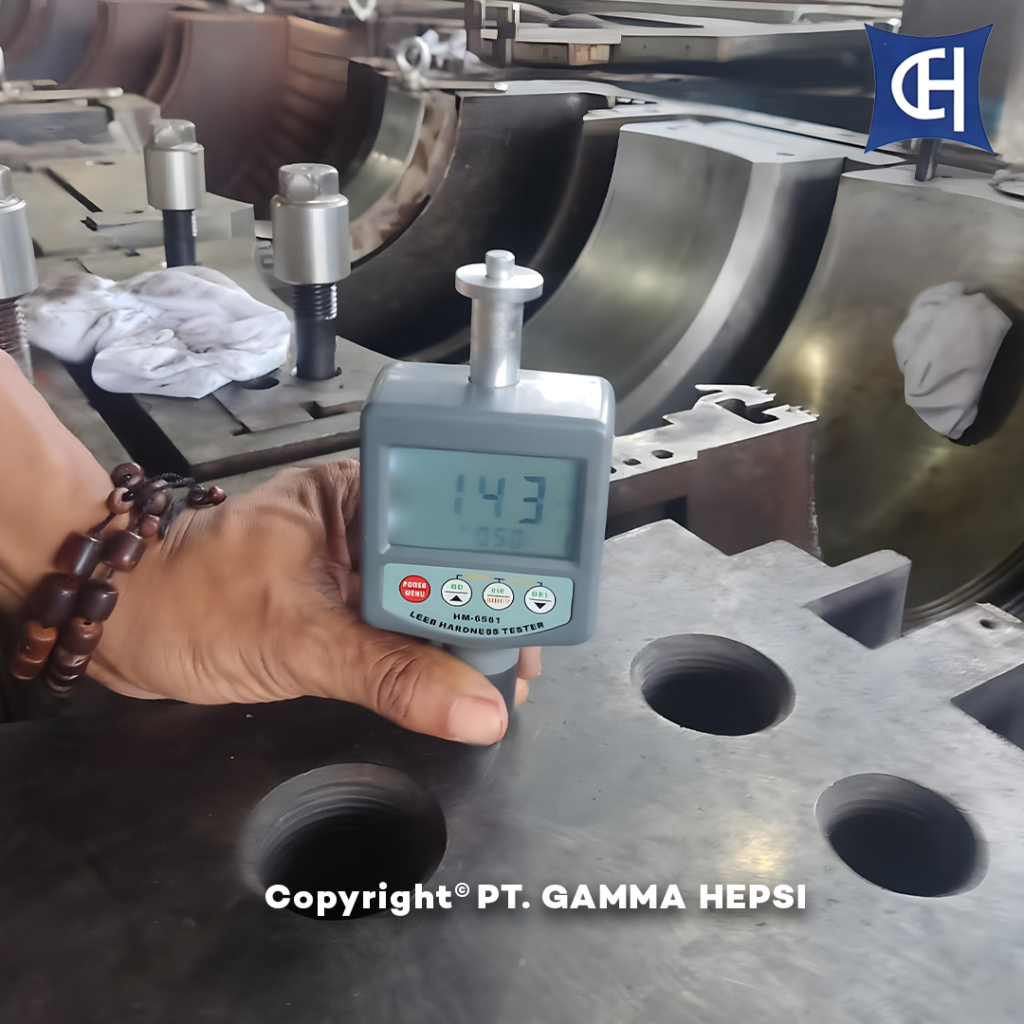
Hardness test
Click for detail
Hardness Testing is a critical non-destructive testing (NDT) method used to assess the hardness of materials, particularly pipes, to evaluate their resistance to indentation, wear, and corrosion. Hardness tests are widely used in industries such as oil and gas, construction, power generation, and manufacturing to ensure the structural integrity and performance of pipes in various applications.
Hardness testing can provide important information about the material properties of pipes, including their strength, ductility, tensile strength, and resistance to wear. These properties are crucial when evaluating pipes for pressure resistance, fatigue resistance, and corrosion resistance, all of which are vital for the safe and reliable operation of pipeline systems
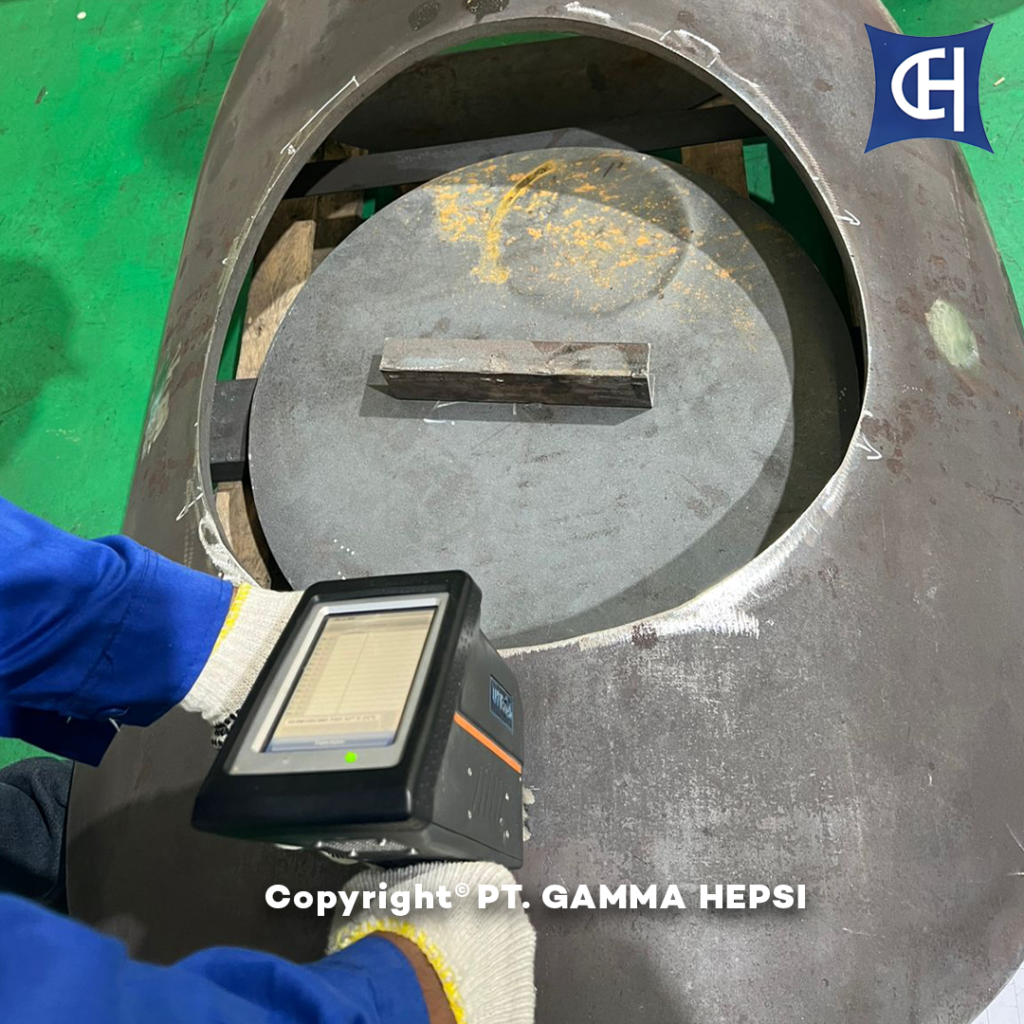
PMI
Click for detail
Positive Material Identification (PMI) is a non-destructive testing (NDT) technique used to determine and verify the chemical composition of materials, particularly metals and alloys, without causing any damage to the material being tested. PMI is essential for ensuring that materials used in critical applications, such as piping systems, pressure vessels, and structural components, conform to the required specifications and standards.
In pipe inspection, PMI plays a crucial role in identifying materials that have been incorrectly substituted, ensuring quality control, safety, and compliance with industry codes and standards. It helps to verify that pipes, fittings, and welds are made from the correct materials, avoiding risks associated with using substandard or incorrect materials in critical applications such as oil and gas, chemical processing, nuclear power, and marine industries.ion of pipeline systems
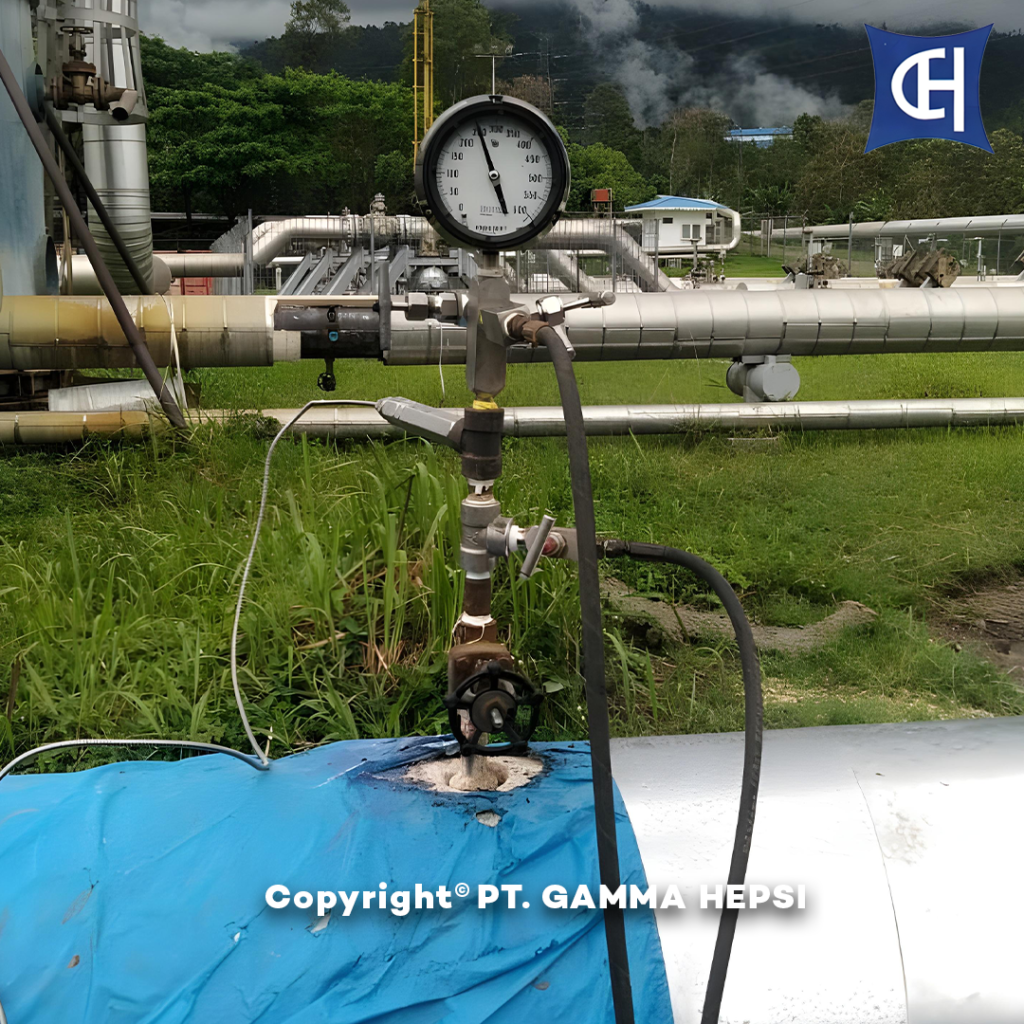
Hydro Test
Click for detail
Hydrostatic testing is a common and essential method used to assess the integrity and strength of pipes, vessels, tanks, and other pressure-related systems. This non-destructive test involves filling the pipe or system with water (often with a small amount of added pressure to test for leaks or weaknesses) and pressurizing it to ensure that it can withstand the designed operating pressures without failing. Hydrostatic testing is particularly crucial for ensuring the safety and reliability of piping systems that operate under high pressure, such as in the oil and gas, chemical, water supply, and nuclear industries.
The process of hydrostatic testing helps to confirm that the pipe or system can withstand the maximum operating pressure and is free of leaks, weaknesses, or defects that could lead to catastrophic failures during normal operation.
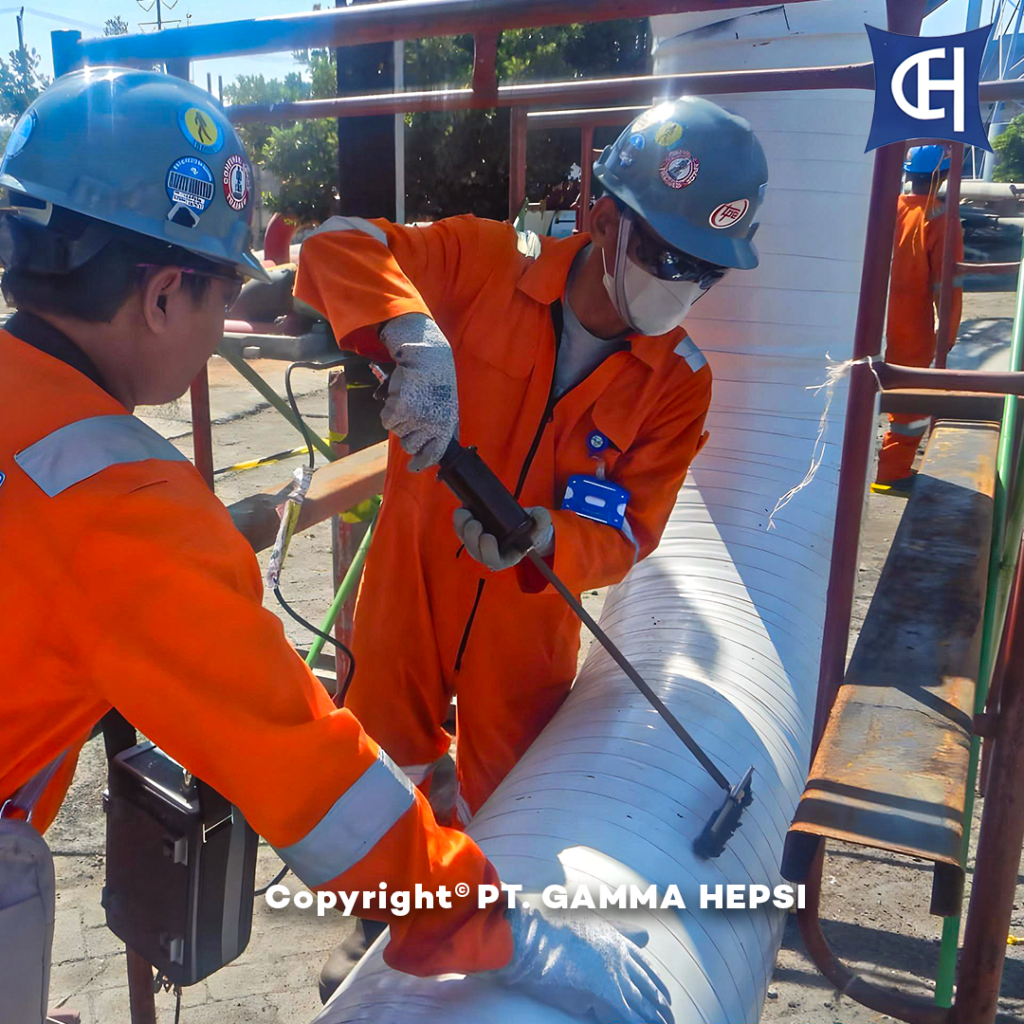
Holiday Detector
Click for detail
Holiday Detector Testing, also known as Holiday Testing or Porosity Testing, is a non-destructive testing (NDT) method used to detect holidays (small discontinuities or defects) in coatings that have been applied to the surface of pipes and other materials. This test is particularly important for ensuring the integrity of protective coatings on pipes, which are crucial for preventing corrosion and ensuring the longevity of pipeline systems, especially those used in oil and gas, water, and chemical industries.
A holiday refers to any uncoated area or pinhole in the coating that could expose the underlying pipe material to corrosive elements, leading to premature degradation or failure. The goal of holiday detection is to identify such defects so they can be repaired before the pipe is put into service.
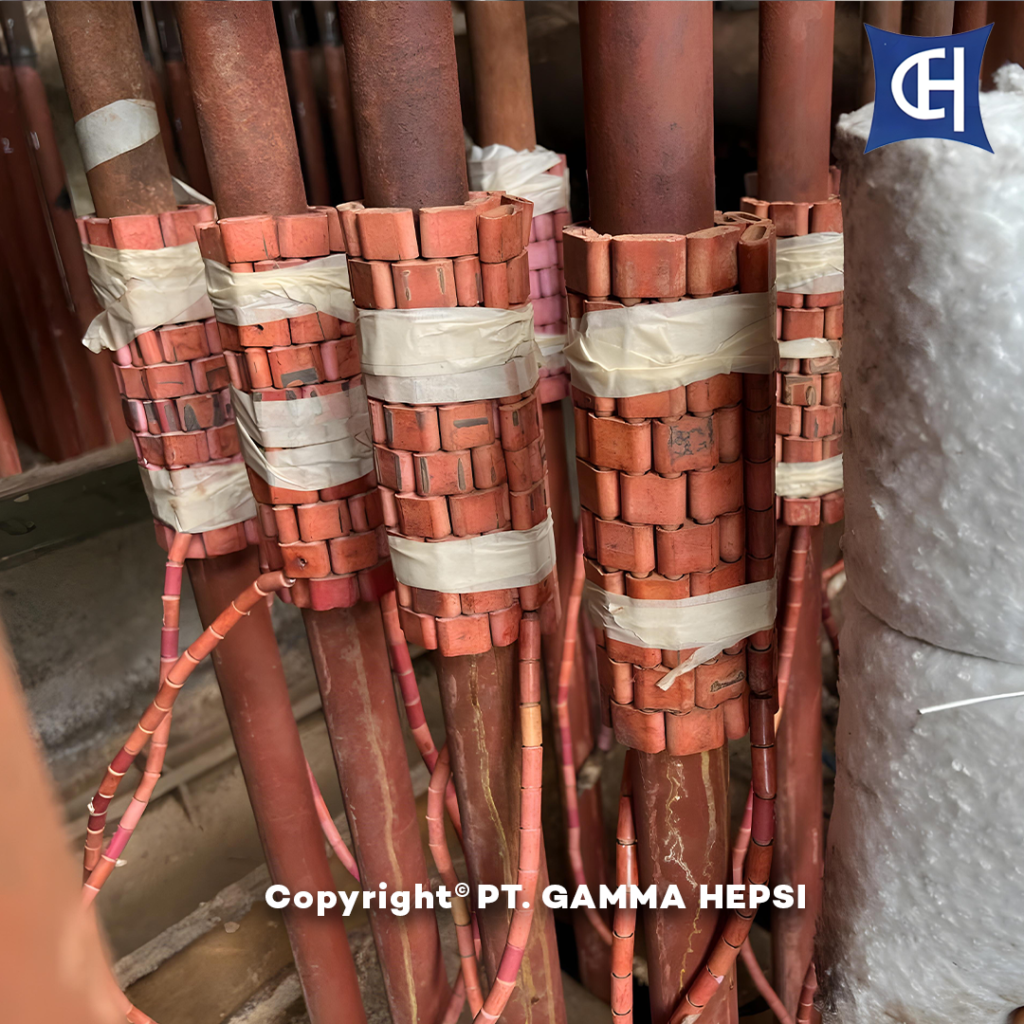
PWHT
Click for detail
Post-Weld Heat Treatment (PWHT) is a heat treatment process applied to welded pipes or other welded structures after the welding process is completed. The purpose of PWHT is to reduce the residual stresses induced by welding, relieve any potential hardness issues, and improve the overall mechanical properties of the welded area, ensuring the integrity and long-term performance of the pipeline or piping system.
Welding, especially on thick-walled pipes, generates high localized temperatures that can lead to residual stresses, cracking, hardness variations, and embrittlement. PWHT is performed to mitigate these issues, enhancing the ductility, toughness, and corrosion resistance of the weld and heat-affected zones (HAZ).
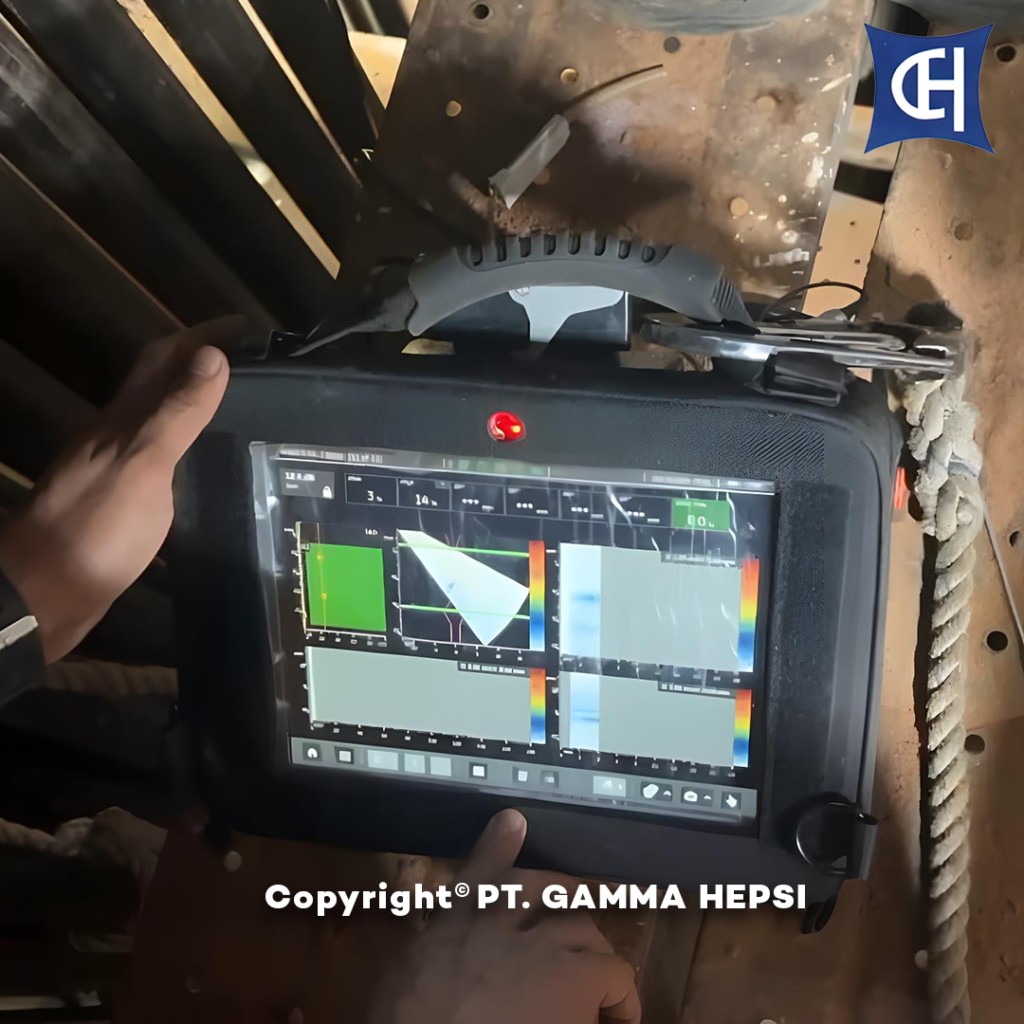
PAUT ( Phased Array Ultrasonic Test )
Click for detail
Phased Array Ultrasonic Testing (PAUT) is an advanced form of Ultrasonic Testing (UT) that uses an array of ultrasonic transducers to generate and receive high-frequency sound waves. Unlike conventional ultrasonic testing that uses a single probe to transmit and receive sound waves, PAUT uses multiple elements (transducers) arranged in a linear or matrix pattern to produce a more detailed and accurate scan of the material being tested. This method enables inspectors to perform complex inspections with higher resolution, improved data collection, and more efficient analysis of welds, materials, or structural components.
PAUT is widely used in industries such as oil and gas, aerospace, nuclear, automotive, and manufacturing, where detecting subsurface flaws like cracks, voids, porosity, or other discontinuities is critical for safety, integrity, and performance.
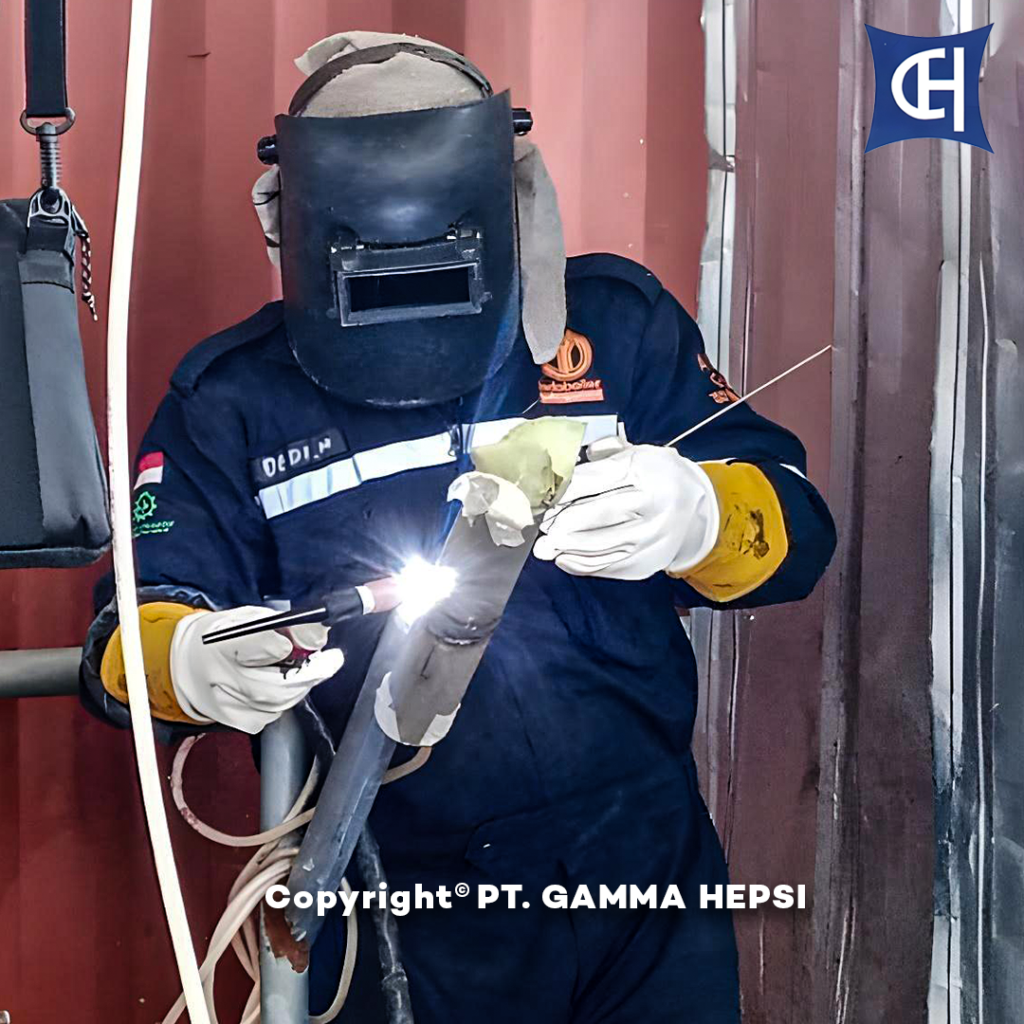
WPS/PQR
Click for detail
In welding, ensuring the quality and integrity of welds is paramount, especially in industries where welded joints are exposed to high stresses, extreme temperatures, or corrosive environments. To standardize welding processes and ensure consistent, high-quality results, welding codes and standards like ASME and AWS require the development and documentation of specific welding procedures. Two critical documents in this process are the Welding Procedure Specification (WPS) and the Procedure Qualification Record (PQR)
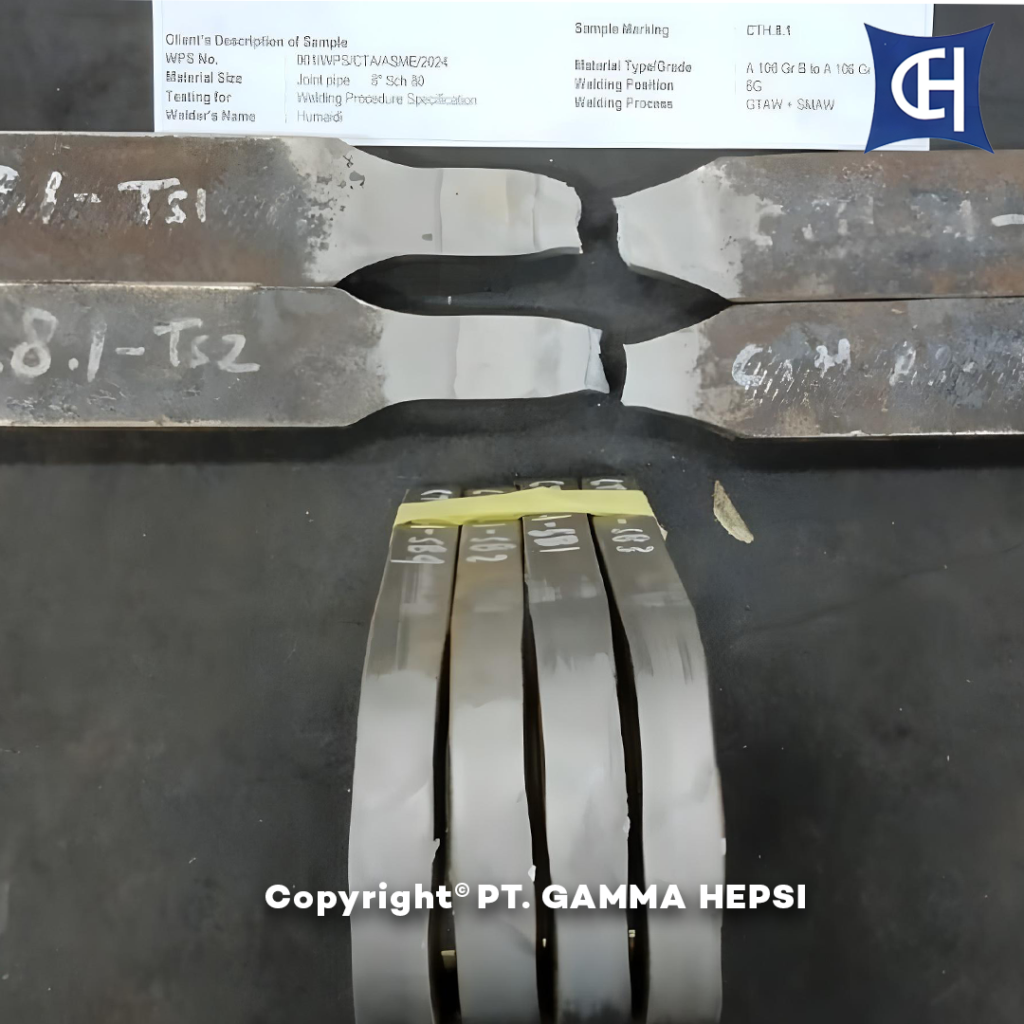
Certification
Click for detail
Pipe inspection is a critical process in industries like oil and gas, petrochemical, nuclear power, and manufacturing, where the integrity of pipelines is vital for safety, performance, and compliance with industry standards. Pipe inspection certification refers to the formal process by which an individual or organization demonstrates competence in the inspection of pipes and piping systems according to industry-recognized standards and codes. Certification ensures that inspectors are qualified to identify, assess, and report any defects, wear, or damage in piping systems, thereby guaranteeing the safety, reliability, and longevity of the infrastructure.
Certification in pipe inspection is typically governed by international standards such as ASME (American Society of Mechanical Engineers), API (American Petroleum Institute), ISO (International Organization for Standardization), and ASNT (American Society for Nondestructive Testing). These organizations set the guidelines and criteria for the qualification of pipe inspection personnel.